摘 要 此次毕业设计任务是对3L-10/8空气压缩机曲轴零件的机械加工工艺、夹具的设计,在曲轴零件的加工工艺过程中轴与轴中心线之间要有位置要求, 以毛坯轴两端定位先加工两中心孔,以两端中心孔定位再粗、精加工各轴的表面,然后以粗、精后的两轴径定位钻螺纹、铣键槽和铣曲拐端面,采用专用夹具加工两斜油孔,最后粗、精磨各轴。 在夹具的设计过程中,主要以V形块和支承板来定位,靠直压板和弹簧来夹紧,钻拐径两孔应采用长型快换钻套,在钻拐径倾斜 的孔时采用平面倾斜的夹具体,在钻拐径倾斜 的孔时使用的是卧式钻床,铣面时2个V形块与铣刀不能干涉,因此V形块高度要降低,夹具设计要方便、简单。
关键词 曲轴,加工工艺,夹具设计。
ABSTRACT
This graduation project duty is to the 3L-10/8 air compressor crank components machine-finishing craft, the jig design, between the crank components processing technological process middle axle and the axle must have the position request ,processes two center bores first by the semifinished materials axis both sides localization ,by both sides center bore localization again thick, precision work various axes surface.Then after thick, the essence two axle diameter localization drills the thread, the keyseat and the mill crank end surface.,uses the unit clamp to process two slanting oil holes, finally thick, correct grinding various axes. In the jig design process, mainly locates by V shape block and the support plate, depends on the straight clamp and the spring clamps, drills turns diameter two to be supposed to use long trades quickly drills the wrap, when drills turns the diameter incline hole uses the plane incline the jig body, when drills turns the diameter incline hole uses is the horizontal-type drilling machine, when face milling 2 V shape blocks and the milling cutter cannot interfere ,therefore V shape block altitude must reduce, the jig design must be convenient, be simple.
Key words crank, processing craft, jig design.
夹具结构设计在加深我们对课程基本理论的理解和加强对解决工程实际问题能力的培养方面发挥着极其重要的作用。选择曲轴的夹具设计能很好的综合考查我们大学四年来所学的知识。本次所选设计内容主要包括:工艺路线的确定,夹具方案的优选,各种图纸的绘制,设计说明书的编写等。机械加工工艺是规定产品或零件机械加工工艺过程和操作方法,是指导生产的重要的技术性文件。它直接关系到产品的质量、生产率及其加工产品的经济效益,生产规模的大小、工艺水平的高低以及解决各种工艺问题的方法和手段都要通过机械加工工艺来体现,因此工艺规程的编制的好坏是生产该产品的质量的重要保证的重要依据。 利用更好的夹具可以保证加工质量,机床夹具的首要任务是保证加工精度,特别是保证被加工工件是加工面与定位面以及被加工表面相互之间的位置精度。提高生产率,降低成本,使用夹具后可以减少划线、找正等辅助时间,且易于实现多工位加工。扩大机床工艺范围,在机床上使用夹具可使加工变得方便,并可扩大机床工艺范围。减轻工人劳动强度,保证生产安全。为了让夹具有更好的发展,夹具行业应加强产、学、研协作的力度,加快用高新技术改造和提升夹具技术水平的步伐,创建夹具专业技术网站,充分利用现代信息和网络技术,与时局进地创新和发展夹具技术。
3 工艺规程设计
3.1确定毛坯的制造形式 零件材料为球球墨铸铁,型号为QT600-3。考虑到空气压缩机曲轴的零件较大,零件比较复杂,应采用铸件。而且投资较少,成本较低,生产周期短。
3.2基面的选择 基面选择是工艺规程设计中的重要工作之一,基面选择的正确与合理,可以使加工质量得到保证,生产率得以提高,不盲目的选择基面。否则,加工工艺过程中会问题百出,更有甚者,还会造成零件的大批报废,使生产无法正常进行。 3.2.1 粗基准选择 在小批生产的条件下,通常都是采取划线找正。所以曲轴加工的第一道工序是钳工划线,划出主轴颈端面的十字中心线以及待加工表面的轮廓线,然后按划线找正将曲轴安装在机床上进行加工。这样兼顾了各部分的加工余量,以减少毛坯的废品率。 3.2.2 精基准的选择 加工曲轴的主轴颈止以及与主轴颈同旋转轴心线的其它配合部分和曲柄外圆弧面、外端面时,同轴类零件外圆表面加工一样,采用辅助精基准-顶针孔。用顶针孔作为精基准,符合基面同一的原则,从而可以保证一次安装中加工的各表面的同轴度或垂直度。对于主轴颈较大而偏心距又较小的曲轴,可以在曲轴两端面上分别各打出两个顶针孔A及B,使用典型的一面两孔定位方法,则可以满足整个加工过程中基本上都采用统一的基准定位的要求。
3.3制定工艺路线 制定工艺路线的出发点,应该是使零件的几何形状、尺寸精度等技术要求能得到合理的保证。除此之外,还应当考虑经济效果,以便使生产成本尽量下降。 工艺路线方案(一): 1)画线,以毛坯外形找正,划主要加工线,偏心距100 mm及外形加工。 2)划轴两端中心孔线,顾各部加工余量。 3)工件平放在镗床工作台上,压轴95 mm两处,钻右端中心孔。 4)夹右端(1:10锥度一边)顶右端中心孔,粗车左端外圆Ø95 mm,粗车左端所有轴径,粗车拐径外侧左、右端面,保证拐径外侧的对称性及尺寸,粗铣凸台Ø25。 5)夹右端,左端上中心架车端面,去长短保证总长尺寸610mm,钻左端中心孔,钻左端Ø6的孔,深16.8mm,锪60°角,深7.8mm,再锪120°角,深1.8mm。 6)粗车拐径Ø95 mm尺寸。 7)精车拐径Ø95 mm尺寸。 8)夹左端,顶右端中心孔,精车右端轴径Ø95 mm,长度尺寸至87mm,保证曲拐端面60mm尺寸,精车右端轴径Ø93至图示长度12mm。 9)夹右端,顶左端中心孔,精车左端轴径Ø95 mm,长度尺寸至85mm,保曲拐端面60mm尺寸。 10)以两中心孔定位,磨左端轴径Ø95 mm,磨左端轴径Ø90 mm。 11)以两中心孔定位,倒头装夹,磨左端轴径Ø95 mm。 12)底面60mm×115mm,以两侧面定位并压紧,保证距中心高70mm,总高236mm。 13)以两轴径定位压紧钻、攻4—M20螺纹。 14)以两端中心孔定位,精磨拐径Ø95 mm至图样尺寸,磨圆角R6。 15)以两端中心孔定位,精磨两轴径Ø95 mm至图样尺寸,磨圆角R6,精磨Ø90 mm至图样尺寸,倒角2.5×45°。 16)夹右端,顶右端中心孔车1:10圆锥,留余量1.5mm 。 17)以两端中心孔定位,磨1:10圆锥Ø86长124mm,磨圆角R6。 18)粉探伤各轴径,拐径。 19)划键槽线24mm×110mm,铣键槽,以两轴径Ø95 mm定位,采用专用工装装夹铣键槽24mm×110mm至图样尺寸。 20)铣右端轴径Ø93mm的槽44 mm至图样尺寸。 21)粗镗、精镗右端Ø30 mm孔至图样尺寸,深75mm。锪60°角,深5.5mm,再锪120°角,深2mm。。 22)重新装夹工件,采用专用工装装夹,钻拐径Ø95 mm两斜油孔Ø8mm。 27)钳工,修油孔,倒角,清污垢。 28)检查。 工艺路线方案(二): 1)画线,以毛坯外形找正,划主要加工线,偏心距100 mm及外形加工。 2)划轴两端中心孔线,顾各部加工余量。 3)工件平放在镗床工作台上,压轴95 mm两处,钻右端中心孔。 4)夹右端(1:10锥度一边)顶右端中心孔,粗车左端外圆Ø95 mm,粗车左端所有轴径,粗车拐径外侧左、右端面,保证拐径外侧的对称性及尺寸,粗铣凸台Ø25。 5)夹右端,左端上中心架车端面,去长短保证总长尺寸610mm,钻左端中心孔,钻左端Ø6的孔,深16.8mm,锪60°角,深7.8mm,再锪120°角,深1.8mm。 6)粗车拐径Ø95 mm尺寸。 7)精车拐径Ø95 mm尺寸。 8)夹左端,顶右端中心孔,精车右端轴径Ø95 mm,长度尺寸至87mm,保证曲拐端面60mm尺寸,精车右端轴径Ø93至图示长度12mm。 9)夹右端,顶左端中心孔,精车左端轴径Ø95 mm,长度尺寸至85mm,保曲拐端面60mm尺寸。 10)以两轴径定位压紧钻、攻4—M20螺纹。 11)粉探伤各轴径,拐径。 12)划键槽线24mm×110mm,铣键槽,以两轴径Ø95 mm定位,采用专用工装装夹铣键槽24mm×110mm至图样尺寸。 13)铣右端轴径Ø93mm的槽44 mm至图样尺寸。 14)粗镗、精镗右端Ø30 mm孔至图样尺寸,深75mm。锪60°角,深5.5mm,再锪120°角,深2mm。。 15)重新装夹工件,采用专用工装装夹,钻拐径Ø95 mm两斜油孔Ø8mm。 16)以两中心孔定位,磨左端轴径Ø95 mm,磨左端轴径Ø90 mm。 17)以两中心孔定位,倒头装夹,磨左端轴径Ø95 mm。 18)底面60mm×115mm,以两侧面定位并压紧,保证距中心高70mm,总高236mm。 19)以两端中心孔定位,精磨拐径Ø95 mm至图样尺寸,磨圆角R6。 20)以两端中心孔定位,精磨两轴径Ø95 mm至图样尺寸,磨圆角R6,精磨Ø90 mm至图样尺寸,倒角2.5×45°。 21)夹右端,顶右端中心孔车1:10圆锥,留余量1.5mm 。 22)以两端中心孔定位,磨1:10圆锥Ø86长124mm,磨圆角R6。 23)钳工,修油孔,倒角,清污垢。 24)检查。 通过两种工艺方案的比较可得出第一种方案中在精磨以后再铣键槽、钻油孔,这样会影响精磨后各轴的加工精度。而第二种方案则比较好些,它在铣键槽、钻油孔后粗、精磨各轴保证了各轴的精度要求。
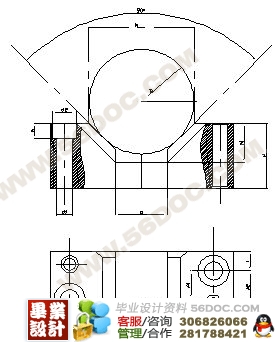
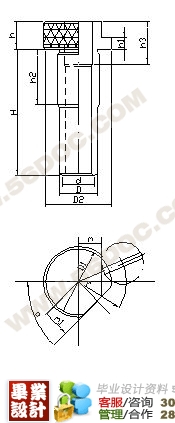
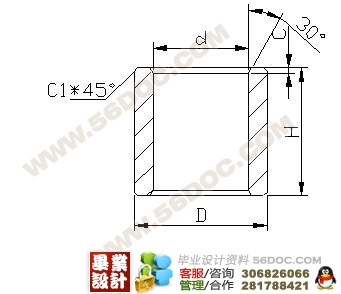
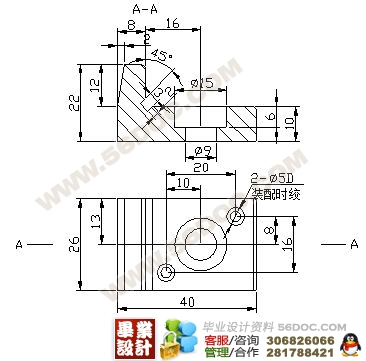
目 录
摘 要 I ABSTRACT I 1 绪 论 1 2 零件分析 2 2.1零件的作用 2 2.2零件的工艺分析 2 2.3零件加工的主要问题和工艺过程设计分析 2 3 工艺规程设计 5 3.1确定毛坯的制造形式 5 3.2基面的选择 5 3.2.1 粗基准选择 5 3.2.2 精基准的选择 5 3.3制定工艺路线 5 3.4机械加工余量、工序尺寸及毛坯尺寸的确定 7 3.5 确定切削用量及基本工时 11 3.6 时间定额计算及生产安排 31 4 专用夹具设计 40 4.1加工曲拐上端面油孔夹具设计 40 4.1.1定位基准的选择 40 4.1.2切削力的计算与夹紧力分析 40 4.1.3夹紧元件及动力装置确定 41 4.1.4钻套、衬套及夹具体设计 42 4.1.5夹具精度分析 44 4.2加工曲拐上侧面油孔夹具设计 45 4.2.1定位基准的选择 45 4.2.2切削力的计算与夹紧力分析 45 4.2.3夹紧元件及动力装置确定 46 4.2.4钻套、衬套及夹具体设计 47 4.2.5夹具精度分析 48 4.3铣曲拐端面夹具设计 49 4.3.1定位基准的选择 49 4.3.2定位元件的设计 49 4.3.3铣削力与夹紧力计算 50 4.3.4对刀块和塞尺设计 51 4 结 论 53 参考文献 54 致 谢 55 |