斜齿轮注射成形工艺与模具(含CAD零件图装配图)(任务书,开题报告,外文翻译,论文说明书13000字,CAD图10张)
摘 要
塑料斜齿轮是化工设备系统中的重要零件,注射工艺是塑料斜齿轮的关键工序,本文是对斜齿轮进行注射塑料模具设计,文中从所给制件的结构尺寸和所用原材料这两方面进行了斜齿轮的注射成型工艺的分析,并进行了模具主要结构形式的设计过程,包括浇注系统的设计、成型零件的结构设计计算、脱模机构的设计等。由于所给的斜齿轮零件中心带有键槽且两端有凸缘,模具采用了齿形型环的旋转脱螺纹机构,使得旋转脱模和抽芯同时进行,缩短了脱模行程,这是本套模具中的一大亮点。在此基础上,对主要零件进行了加工工艺的分析,并对塑件进行了模流分析以获得最好的注射成型效果。通过模具各个系统的结构设计并校核相关模具尺寸,从而完成了整体模具的设计过程并且实现了斜齿轮的注射成型。
关键词:斜齿轮;注射成型;模具设计;工艺性分析
Abstract
Plastic helical gear is one of the most important parts in chemical equipment system, the injection process is the key in the process of plastic helical gear, this paper is plastic injection mold design of the helical gear, the paper This paper analyzes the process of helical gear injection from the structure and size of the parts and raw materials , and the design process of the main structure of the mold was carried out, including the design of gating system, the structure design and calculation of molding parts, demoulding mechanism design and so on. Due to the helical gear parts center with key grooves, and both ends of the flange, the mould adopts the dentiform ring spinning thread demoulding mechanism, making the rotation of the mold and core pulling at the same time, shorten the release schedule, which is the set of die is a major highlight of the mould. On this basis, the main parts of the processing process and plastic parts of the mold flow is analyzed to obtain the best effect of injection molding. The die structure design of each system and check related die size, thus completing the whole design process of the mold and the realization of the cable gear injection molding.
Keyword:helical gear; injection molding; mold design;;process analysis
2.4塑件结构工艺性分析
选用合适的原材料是得到优良的塑料制件的前提,此外,还必须考虑塑件结构的工艺性,考虑塑件结构工艺性,需要遵守以下原则:
⑴在设计之初,必须将收缩率、流动性等将原材料的结构工艺性考虑在内。
⑵在保证塑件的性能,物理性能和力学性能,耐化学性,耐热性和电性能,如要求的前提下,尽可能的厚度均匀,结构简单,使用方便。
⑶设计时需考虑模具的总体布局结构,使模具的抽芯和推出机构简易和模具型腔制造方便。
⑷如果想要得到外观质量较高的塑件,需要首先对塑件进行造型,对不合理的结构进行完善,然后再对图样进行绘制。
3.1 型腔数目的确定
从零件图2-1、2-1中可以看出,该零件是两端带凸缘的斜齿轮组件,虽然形状简单,结构合理且制件的壁厚均匀,在成型时塑料在模具型腔内流动阻力相对较小有利于制品的成型。但其与普通的斜齿轮不同,该斜齿轮的中心带有键槽,其齿槽方向与开模方向不一致,不能直接对塑件进行脱模,因此需要设计一个旋转的脱模机构来实现脱模过程。此外,考虑到脱模时齿轮中心的键槽不能旋转,因而对于模具脱模结构的设计具有一定的难度。
注射模的型腔数目可以是一模一腔或一模多腔,采用不同的型腔数目各有优缺点。从零件图及所给的数据可以看出,此塑件的精度要求不高,生产批量适中,而且塑件需要进行旋转脱模,脱模机构相对复杂,同时考虑到制品生产及模具的加工成本,在此模具中型腔数目采用一模一腔。
3.2 分型面位置的确定
一般情况下,分型面位置设置应遵循有得于制品脱模、开模后制品滞留在动模一侧、降低模具加工难度等原则,通过对塑件结构形式的分析,为保证成型质量,分型面应选在端盖截面积最大且利于开模取出塑件的位置,且因为该塑件的中间部位为斜齿轮,为了更好地顺利实现脱模
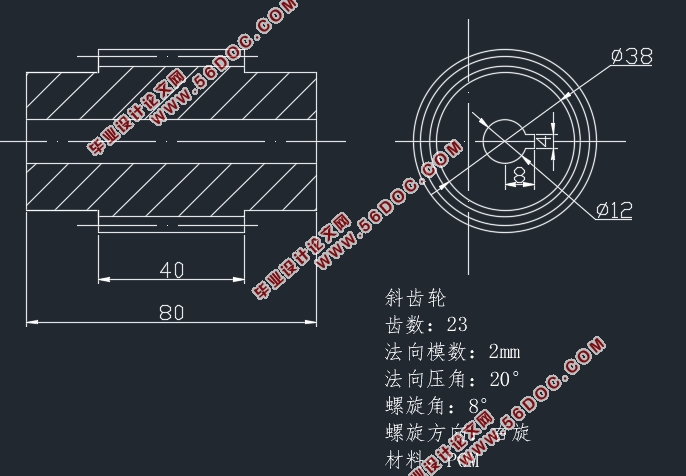
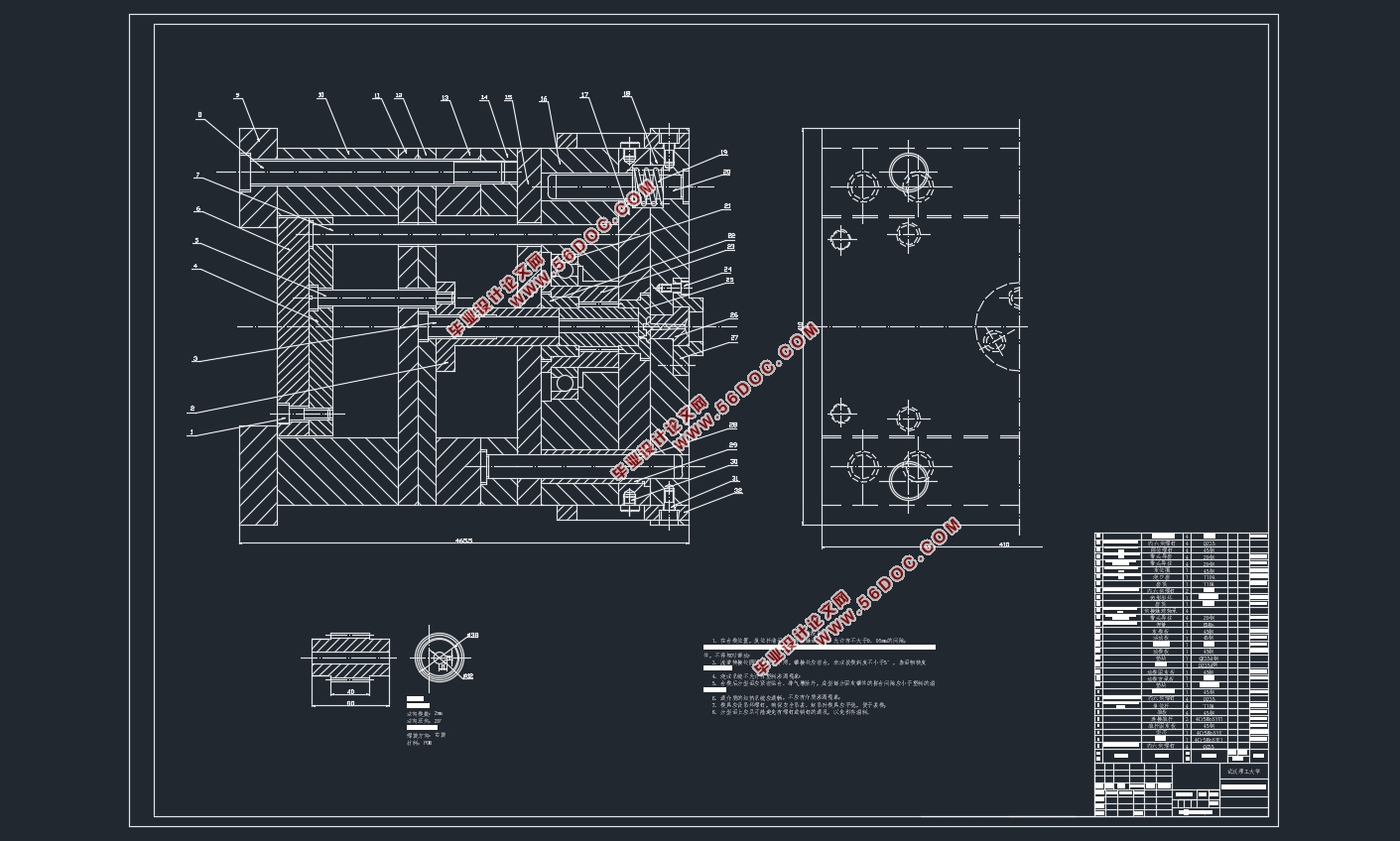
目 录
第1章 绪论 1
第2章 塑件(斜齿轮)的分析 2
2.1 斜齿轮塑件的模型及参数 2
2.2 塑料的基础知识与应用 3
2.3 聚甲醛(POM)的性能分析 3
2.3.1 聚甲醛(POM)的工艺性能 3
2.3.2 聚甲醛(POM)的成型特性 4
2.3.3 聚甲醛(POM)的成型的基本性能 4
2.4 塑件结构工艺性分析 4
第3章 模具结构形式的拟定 6
3.1 型腔数目的确定 6
3.2 分型面位置的确定 6
3.3 注射机型号的确定 6
3.3.1 注射量的计算 6
3.3.2 浇注系统凝料体积的初步估算 7
3.3.3 注射机的选择 7
第4章 浇注系统的设计 8
4.1 主流道的设计 8
4.2 分流道的设计 9
4.3 浇口的设计 9
4.3.1 浇口位置 9
4.3.2 浇口结构形式 9
4.4 主流道浇口套的形式 10
4.5 定位圈的选用 10
第5章 成型零件的结构设计及计算 11
5.1 成型零件的结构设计 11
5.1.1 成型凹模的结构设计 11
5.1.2 成型凸模的结构设计 11
5.2 成型零件工作尺寸的计算 11
5.2.1 齿形型环工作尺寸的计算 12
5.2.2 套筒工作尺寸的计算 12
5.2.3 型芯工作尺寸的计算 12
第6章 注塑模具的模流分析 14
6.1 零件三维模型的建立 14
6.2 塑件浇注系统的建立 14
6.3 塑件的模流分析 15
第7章 脱模机构的设计 19
7.1 推管推出机构 19
7.2 连接推杆的设计 20
7.3 定距拉板的设计 20
第8章 复位机构及合模导向机构的设计 21
8.1 复位杆的设计 21
8.2 合模导向机构的设计 21
第9章 温度调节系统及排气结构的设计 23
9.1 模具温度调节对塑件温度的影响 23
9.2 冷却系统的设计 23
9.2.1 塑料传给模具的热量 23
9.2.2 模具散发的热量 23
9.3 加热系统的设计 24
9.4 排气结构的设计 25
第10章 模具有关尺寸的校核 26
10.1 注射机的校核 26
10.1.1 喷嘴尺寸校核 26
10.1.2 闭合高度校核 26
10.1.3 模具外形尺寸校核 26
10.1.4 固定螺孔校核 26
10.1.5 最大行程的校核 27
10.1.6 脱模力的计算校核 27
10.1.7 锁模力的计算校核 28
10.2 凹模侧壁强度与刚度的设计校核 28
10.2.1 齿形型环的设计校核 28
10.2.2 套筒的设计校核 29
10.3 型芯的强度与刚度设计校核 29
10.4 动模支承板厚度设计 30
结论 31
致谢 32
参考文献 33
|